The spray gun is a critical component in any coating or foaming process. Its performance directly affects product quality and production efficiency. However, spray gun clogging is a common issue that can lead to uneven spraying, downtime, and equipment damage. This article provides a comprehensive overview of the causes of spray gun clogging and effective preventive maintenance measures.
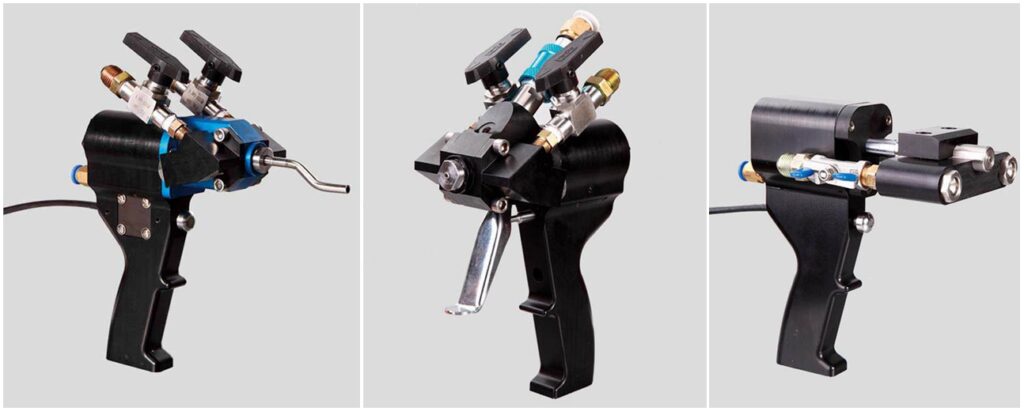
Common Causes of Spray Gun Clogging
Foreign Objects Entering the Nozzle
During operation, accidental drops or improper handling may cause foreign materials to enter the nozzle. Minor blockages can be cleared by removing the obstruction, but if the nozzle or internal parts are damaged, replacement may be necessary.
Inadequate Cleaning After Use
If the spray gun is not cleaned thoroughly after use, residual material inside can solidify and cause blockages in the nozzle or internal channels. Hardened material not only blocks flow but may also damage precision components.
Raw Material Issues
Improper mixing ratios, contamination, or the use of materials with significantly different viscosities can lead to premature curing or buildup inside the spray gun. This is especially critical for reactive systems like polyurethane, where precise mixing and flow are essential.
Signs and Effects of Clogging
- Uneven Spraying: Irregular spray patterns, inconsistent coating thickness, or spitting.
- Unexpected Downtime: Clogged guns can halt operations, increasing labor and delay costs.
- System Pressure Issues: Backpressure or system overloads can occur, affecting pump or line performance.
- Defective Output: Surface defects such as pinholes, blotches, or particles in the coating.
Preventive Measures Against Clogging
Cleaning Procedure After Use
A consistent cleaning routine is key to preventing clogging:
- Turn off compressed air and power;
- Empty remaining material from the container;
- Disassemble and clean the spray head with a recommended solvent;
- Use only soft brushes—never metal or hard tools—to avoid damaging the nozzle;
- Wipe down the gun body to remove surface residue.
Daily Operation Best Practices
- Avoid dropping or exposing the spray gun to dust and debris;
- Regularly inspect and replace wear parts like nozzles and seals;
- Check spray flow and pressure before each use;
- Ensure accurate proportioning when using two-component materials;
- Preheat materials when necessary to reduce viscosity and improve flow.
Common Spray System Issues and Solutions
Problem | Likely Cause | Recommended Action |
Spray gun clogging | Foreign matter, hardened material | Disassemble and clean gun, replace nozzle if needed |
Uneven spray | Worn nozzle, pressure instability | Replace nozzle, check pressure regulator and pump |
Material leakage | Loose connections, worn seals | Tighten fittings or replace seals |
Startup failure | Power or motor fault | Inspect power source, wiring, and motor |
Heating failure | Faulty heater or thermostat | Test and replace defective components |
Conclusion
Although spray gun clogging is a common challenge, it can be minimized with proper maintenance, accurate material handling, and regular equipment inspection. Establishing a consistent cleaning routine and understanding the causes of clogging will extend the life of your spray equipment and improve overall product quality.
If you encounter difficulties during spray gun maintenance, feel free to contact our technical support team—we’re here to provide expert guidance and solutions.